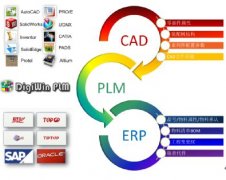
重型装备研发型制造企业PLM系统的关键技术(上
重型装备具有种类多、生命周期长、设计验证难度大、针对性强、运行环境与状态复杂等特点。 研发与制造企业经常面临着产品定制设计、产品品种多样化、设计资料版本管理乱、产品资料数
重型装备具有种类多、生命周期长、设计验证难度大、针对性强、运行环境与状态复杂等特点。 研发与制造企业经常面临着产品定制设计、产品品种多样化、设计资料版本管理乱、产品资料数据同源性难以保证、协同设计效率低、项目管理失控等现实问题。企业虽然已经有CAD、CAM、ERP等局部信息化工具 或系统,但各个系统间缺乏有效衔接,缺乏顶层设计, 实施效果不理想。
PLM(Product Life-cycle Management)系统称之为产品全生命周期管理系统,它是通过信息化管理支持平台,对产品从创建到使用,更新到换代等全生命周期进行管理,能够有效解决重型装备研发与制造企业所面临的问题。
PLM的核心是产品数据的有序管理、设计过程的优化和资源的共享,是支持快速研发 过程的协同管理的一个集成协同框架,在企业内部(可以是分散在多个地点的企业内部),支持产品全生命周期的信息的创建、管理、分发和应用,它能够 集成与产品相关的人力资源、流程、应用系统和信息。笔者针对重型装备研发制造企业的特点,对PLM系统几个关键集成技术进行探讨。
1 重型装备研发型制造企业的研制与经营特点
重型装备作为高端装备,广泛应用于能源、交通、船舶、工程机械、冶金、航空航天、军工等重点行业和领域。 重型装备研制周期长,阶段复杂,包括前期 调研、设计、制造、采购、配套、安装、调试、交付及质量 控制与售后服务等,在这些过程中会产生大量的数据。
通常重型装备技术含量高,其制造需要较多的专用设备,因此,企业的经营更适合采用重研发、轻制造的经营模式,即企业在掌握和控制核心技术的前提 下,主要依赖社会优质资源来实现制造。 这种模式虽 然有利于成本的控制,但给产品的全生命周期数据管 理带来许多问题。 其主要特点概括如下。
(1) 个性化定制。 重型装备大多数属于专用设 备,用户一般都有自己的工艺要求,变型设计类型相对较多,非标与定制特征明显。 虽然每个产品都需要 重新设计,但设计对象的产品族特点明显。 通常变型 产品在企业整个产品的设计制造中占有绝对比例,企 业需要最大程度地利用定制产品之间在设计和制造工艺上的相似性提高设计效率和生产效率。
(2) 产品生命周期链不完整,但关注点突出。 重型装备研发型制造企业通常研发设计能力较强,生产制造能力相对较弱,企业关注的是对核心技术的掌控以及最终完成产品成套,其制造加工过程通过外协、外购来完成。除此之外,企业确实难以完成的某些关 键技术还需要外包。 因此,企业所掌握的产品全生命 周期数据链并不完整。
(3) 高度重视协同设计。为获得市场竞争优势、适应市场需求的快速变化,企业的研发组织结构已经由过去的物理集中向物理分散转变,无论在企业内部或外部,本地或异地,研发、设计、制造需要多家单位、不同机构之间的交流与并行工作,企业需要克服时间、空间等限制,形成一个便于群体相互协同工作的 共同工作空间,使异地多部门、多单位人员能够并行协同地完成工作,这种转变只能依靠信息化系统 支持才能实现。
2 重型装备研发型制造企业面临的主要问题
在市场经济环境下,重型装备研发型制造企业是按订单设计制造。 产品类型多,项目阶段多,并行项 目多,造成研发管理比较复杂,通常面临的主要问题如下。
(1) 难以保证产品数据的一致性
①产品数据版本信息管理不完善,缺乏过程版本,可追溯性差;
②技术文件审核过程中,纸质文档与电子文档分离并同时 存在,一致性难以保证;
③图纸查找困难,设计人员大量的时间花费在数据查找上;
④安全保密无法保障, 产品全部数据虽说存放在计算机中,但数据易受到非法的调用、复制、修改。
(2) 产品结构依靠手工管理:
①需要手工整理产品结构信息,容易出现错误且效率低下;
②产品结构 没有版本控制;
③零部件的替代关系没有有效地管理,不能有效地判断零部件对应的替代件。
(3) 缺乏规范的编码体系,难以保证零件信息的 准确性:
①同一个零件在不同的项目中可能有多个编码值存在,导致编码需要专门人员进行匹配识别;
②编 码新增申请过程难以校验,可能出现重复申请,存在一码多物;
③编码的创建过程依靠手工操作,易产生导致 数据不规范、不一致的情况。
(4) 流程管理费时耗力:最大的问题是管理以纸 质为准,流程执行时间过长。
(5) 更改管理难以控制,差错较多:
①缺乏信息 化系统支持的变更流程,变更请求和变更单多数仍为 纸介质,传递、更改过程耗时长,并且经常造成数据错 误;
②对变更历史缺乏有效的管理,不能有效地对 变更进行追溯,缺乏对产品数据关联关系的有效管理;
③变更控制不严,导致设计过程和制造过程中频 繁出现变更,耗费了大量的时间和人力上的成本。
(6) 项目管理水平较低,计划能力不强,执行效果较差:
①项目计划的管控模式无法支撑项目的全周 期管控,设计、生产、质量等各种计划数据流之间存在断点;
②项目计划难以与最终的交付物进行紧密关联,无法准确监控项目中每一个项目成员或节点的进 度和任务执行情况;
③现有管理模式无法支撑多项目 监控与资源的平衡,多项目的执行情况没有可及时更 新的统计图表,无法同时对比分析多项目的执行情况;
④缺乏项目组人员工作负荷的统计监控,无法对工作量、工作强度进行平衡;
⑤现有管理模式无法支撑项目风险的管控,缺乏项目风险的定义、分类和预警,无法在项目的关键节点、瓶颈资源处对已知风险 做出提示。
上述问题反映了重型装备研发型制造企业对 PLM系统的期望,即:统一和规范数据管理,建立完善的数据管理机制;统一变更管理和流程管理,固化业务流程,增强流程的反馈和查询;规范设计方法;加强知识的共享与重用,研发人员可以方便的进行数据查询和应用。
本文章来自上海御云信息有限公司 : 本文网址:http://www.plmpdm.cn/zxplm/360.html
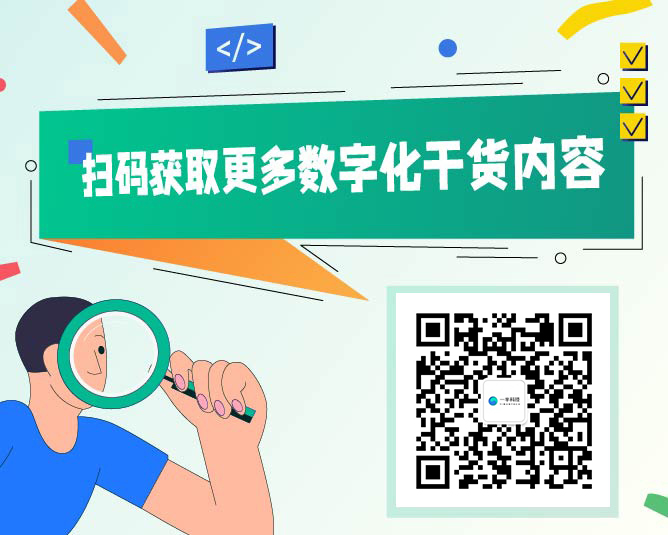